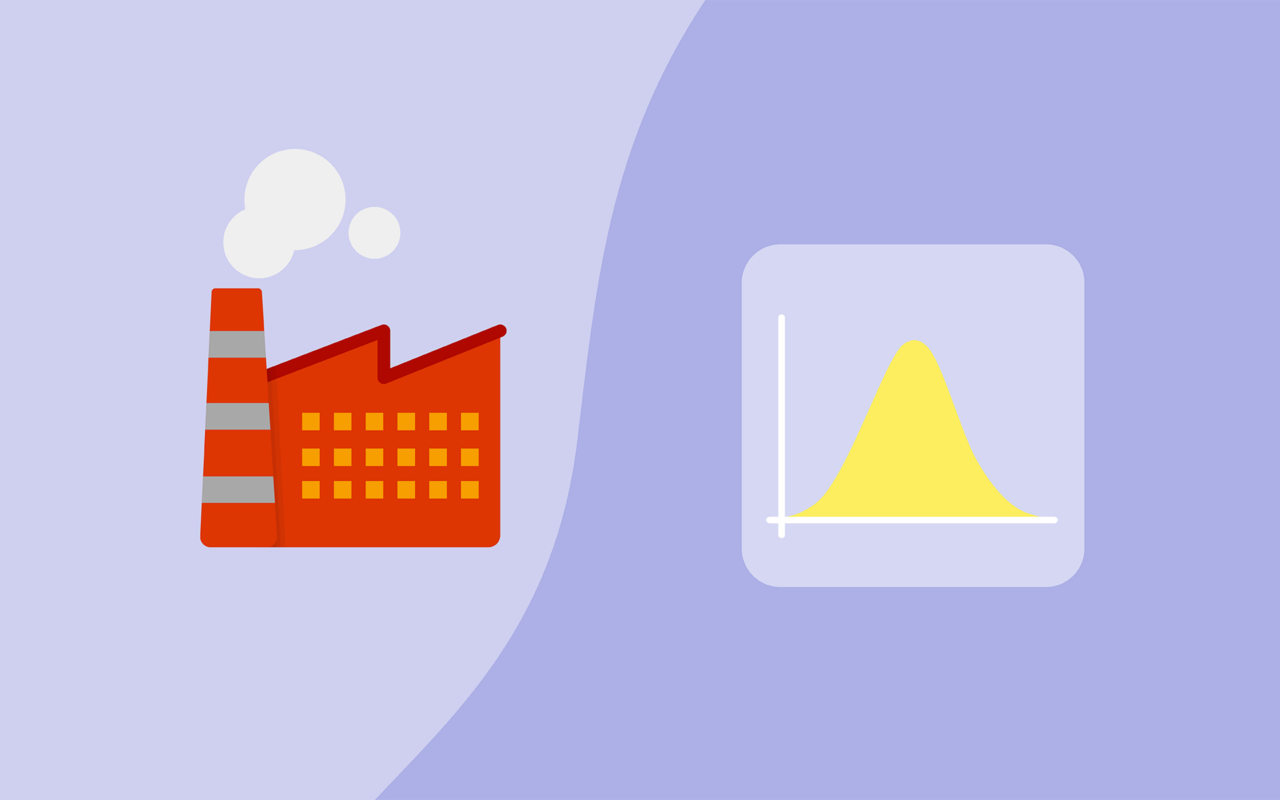
Six Sigma (6σ) refers to a set of techniques and tools that are used to improve the quality of business processes by reducing the number of errors that occur throughout those processes. The methodology was initially developed for use in manufacturing but was rapidly adapted for use in any process that involves both an input and an output.
The goal of Six Sigma is to achieve continuous improvement by identifying and eliminating faults through the application of statistical analysis in real-world settings.
In this post, we’ll delve into the specifics of what Six Sigma is, as well as its history and how it came to be one of the practices that are most widely used around the world to optimize processes. In addition to this, we will investigate its relationship to the Lean methodology and the different certifications that revolve around Six Sigma.
The Origin of Six Sigma
Six Sigma was developed by Bill Smith at Motorola in the early 1980s to measure defects and improve product and service quality. This initial concept remains the foundation of Six Sigma techniques, with a few changes, such as enhancing the process in terms of interaction and product design.
The name Six Sigma originates from the normal distribution curve and the standard deviations associated with it. For a process to be deemed as Six Sigma, the variations in the process should not be more than six standard deviations from the process average.
Each of these deviations is marked by the Greek character “sigma” and since it’s six of them, this is where the name Six Sigma (6σ) comes from.
The objective of the Six Sigma quality management system is to achieve a defect rate of 3.4 or lower for every million possible outcomes. Therefore, quite close to perfection.
Source: Researchgate.net
General Electric (GE) was the first company to implement Six Sigma on a large scale to decrease waste, increase product quality, and save money. People began implementing Six Sigma programs in various firms as a result of GE's accomplishments.
Today, businesses all around the world employ Six Sigma to enhance processes, which facilitates positive organizational transformations.
What is Six Sigma?
The Six Sigma methodology places a strong emphasis on the customer, with the goal of providing superior quality, value, and reliability to the end user.
Six Sigma, in its most fundamental form, seeks to maximize financial savings by cutting down on the number of errors that occur during a process. The greater the number of flaws in a process, the greater the amount of money that is wasted.
But how do you translate the goal of Six Sigma into real-world applications? When you’re in the office and strategizing, where do you look for guidance?
The best way to understand Six Sigma is to understand the principles that guide it. Let’s take a look:
The 5 Key Principles of Six Sigma
1. Serving the customer
The primary purpose of any change in the manufacturing process should be to maximize customer benefit. Establishing a clear quality standard early on determines what the customer/market expects.
2. Identifying and concentrating on obstacles
It's easy to get caught up in the tornado of changes during the implementation phase and lose sight of the original problem. Gathering data that shows the source of a specific problem allows you to focus on addressing that issue directly.
3. Getting rid of variations and bottlenecks
Once the problem has been discovered, it’s time to look for strategies to eliminate defects. These strategies include defect detection and the consequent steps to remove said defects. This is just like any other quality management system found in industry. These functions can be streamlined to improve quality control and efficiency.
4. Clear communication and team training
A fundamental requirement for a Six Sigma approach to succeed is that all team members understand the aim and are kept up to date on the project's progress. The methodology can cause a significant shift in work environments because it demands specialized management and attention to execute the full process smoothly.
5. Flexibility and responsiveness
Innovation and Six Sigma go hand in hand. It's a procedure that finds flaws and attempts to improve them. For a Six Sigma specialist, clinging to a failed method is not an option. Change may appear difficult at first, but it will have a significant impact on business in the future.
The DMAIC Method
Within Six Sigma exists several techniques that guide the practice of continuous improvement. DMAIC is one of, if not the most important.
Source: Sixsigmadsi.com
The DMAIC method is a simple, yet efficient tool that provides structure and allows teams to identify problems, find solutions and create control methods quickly for improved processing.
How Does Six Sigma Relate to Lean Manufacturing?
Lean is a well-known practice in the manufacturing industry that aims to remove waste from processes. Like Six Sigma, Lean has the objective of saving money by reducing the defects in a process. Before long, companies realized the benefits of the synergy between the two methodologies and formed a combination known as Lean Six Sigma.
A brief comparison is given below:
Lean | Six Sigma | |
Philosophy | Reduces waste in a process | Reduces variation in a process |
Focus | Process flow optimization | Problem-solving |
Primary Result | Reduces flow time | Uniform process output (no defects) |
Secondary Result | Less waste, improves efficiency, reduces cost | Less waste, improves quality, reduces cost |
Lean Six Sigma is thus an approach to process improvement that prioritizes the prevention of errors over the detection of existing ones. It accomplishes this by cutting down on waste and cycle time and promoting the utilization of work standardization and flow, which ultimately results in an advantage over the competition.
Six Sigma Certifications
To fully grasp the concept of Six Sigma, individuals need to go through additional training. There are many layers to the techniques and methodologies used in Six Sigma. Thus, there are different levels of certifications that one can receive.
The certifications are similar to the form used in Taekwondo-Karate with the presentation of ‘belts’. Several organizations provide training, and many manufacturers have built their own internal programs to provide the same service to employees.
The certification belts are as follows:
- White Belt: This is the entry-level course that serves as an introduction to Six Sigma for those who are new to the industry.
- Yellow Belt: Explores the fundamentals and the essentials in greater depth.
- Green Belt: An intermediate-level training program that gets you ready to work on process improvement initiatives within an organization.
- Black Belt: An advanced level of training that focuses on preparing you to manage and direct project teams.
- Master Black Belt: A prestigious training program that helps you develop the skills necessary to instruct others and become an expert in your field.
Closing Thoughts
Those who appreciate finding solutions to problems will find that learning and understanding Six Sigma is a fantastic challenge. In the realm of Six Sigma, there is a great deal more to be discovered, and the potential applications are virtually limitless.
Although you should use the many strategies and procedures as a solid foundation for your problem-solving, it is essential to be aware that each process is distinct in the challenges it presents and how it can be overcome. Therefore, to adapt Six Sigma to your process, you need to include some of your own innovativity.